Evolution of Vehicle Architecture
The evolution of electronics brings vehicle architecture to a turning point
Ah, the 1957 Chevy Bel Air.
Not only a beauty on the outside, but a paragon of simplicity on the inside—at least when it comes to its electrical system. Very, very simple. But as vehicles have evolved over time, so has the electrical
architecture.
Jump ahead to 2018 where the car needs to transfer 15,000 pieces of data in the blink of an eye. Within just a couple of years, by 2020, that will jump to 100,000 pieces of data.
Consumer demand for safety and software-enabled features is increasing at an unprecedented rate. This increase in software-enabled capability impacts infotainment, user experience, active safety and connected vehicle services, and paves the way for the ultimate application, autonomous driving.
As the demand for software-enabled features grows, there is a corresponding increase in the need for computing horsepower. Just like the latest iPhone has to add more computing power to run all the new apps, we need to add more computing horsepower to the car to run all the latest features.
What this means is that the traditional architecture approach will no longer be viable and support the growth in content and complexity. There isn’t enough computing power to run the vehicle’s complex software algorithms, and the networking infrastructure cannot support the data transfer speeds of the future.
A closer look at how electrical architecture systems have evolved over the decades helps explain this remarkable increase—and why the automotive world is shifting from a fragmented approach to the future… a software-defined digital platform.
1950s: Simplicity
Minimal Electrical Content, No Electronics
- 12-volt systems reign
- Ring terminals = primary connection method
- 56/58/59 connections make their debut
- Woven cloth coverings are standard
1960s: Stability
Electrical Content Grows
- Audio and lighting enhancements spur content growth
- Glass fuse protections becomes standard
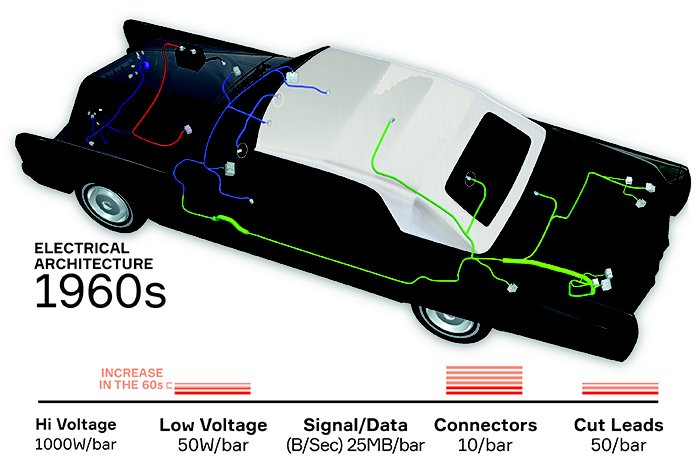
1970s: Anticipation
Electronics Join the Party
- Emission requirements emerge, electronic modules follow
- Circuit protection migrates to smaller footprint auto fuse (ATO)
- Harness positioning begins to require systems expertise
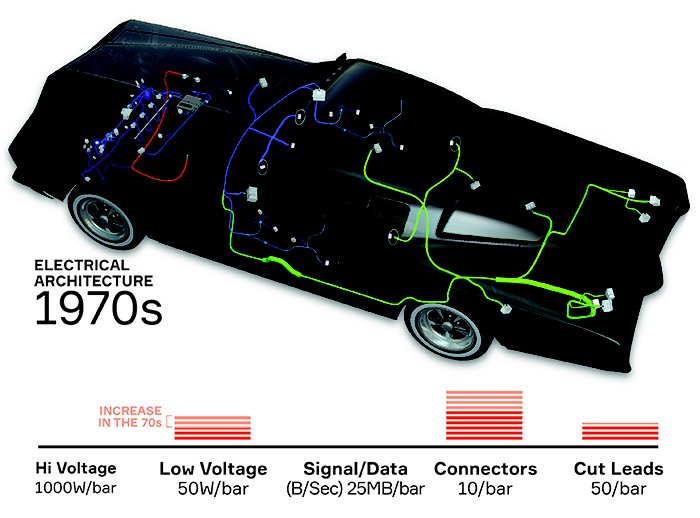
1980s: Take Off
Electronics Integration Means Electrical Growth
- New regulations drive more electrical content
- Sealed connections become best practice
- Electrical partitioning and packaging reach new levels
- Electrical content growth fuels vehicle assembly plant concerns

1990s: Acceleration
Architecture Expertise Becomes a "Thing"
- Electrical centers redefine architecture standards and optimization
- Complexity management becomes vehicle assembly plant focus
- Cable and components miniaturization improves packaging
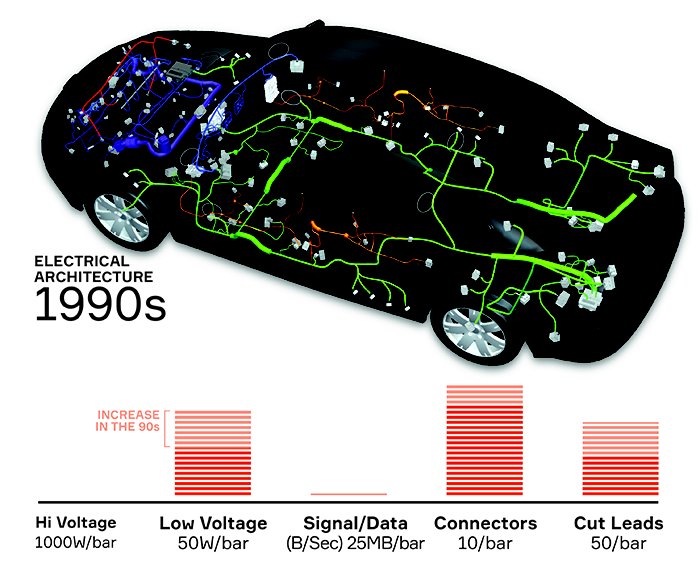
2000s: More and More
Electronics Feed the Features/Functions Beast
- Data and communication protocols drive new product requirements
- “Optional” equipment becomes standard
- More legislation = more content growth
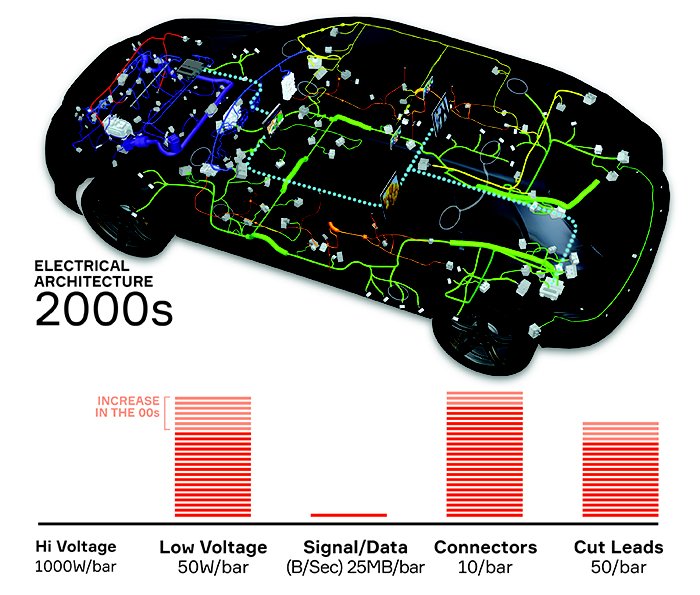
2010s: Connectivity and Safety
High-Power Management Takes Charge
- Consumer electronics integration adds layers of complexity
- Driver distraction becomes a social issue
- Occupant safety spurs additional electrical content
- U.S. fuel economy regulations drive high-voltage powertrains and systems
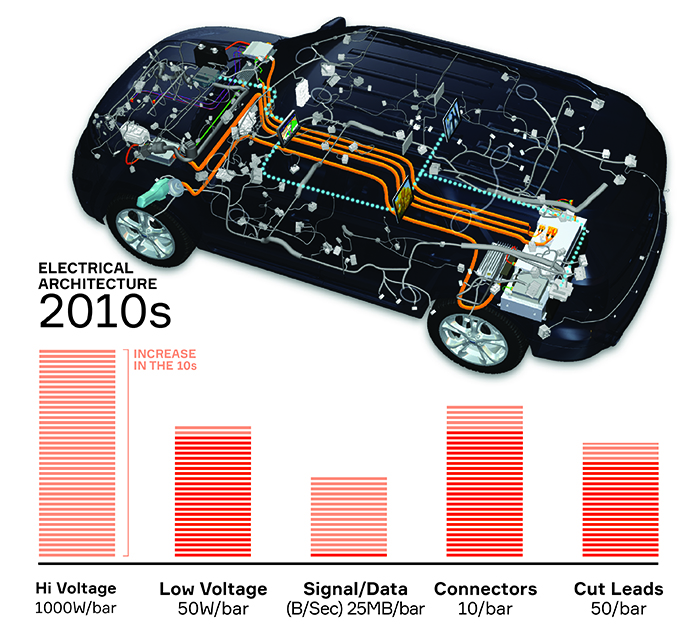
2020s: Mobilization
On-Board Systems Are No Longer the Limit
- Advanced connectivity and safety continue to drive next generation cables/connections
- Legislation (safety, fuel economy, etc.) influences electrical growth and content
- Advanced communication protocols beget new technologies
- Cybersecurity concerns drive multi layers of redundancy and fault tolerances
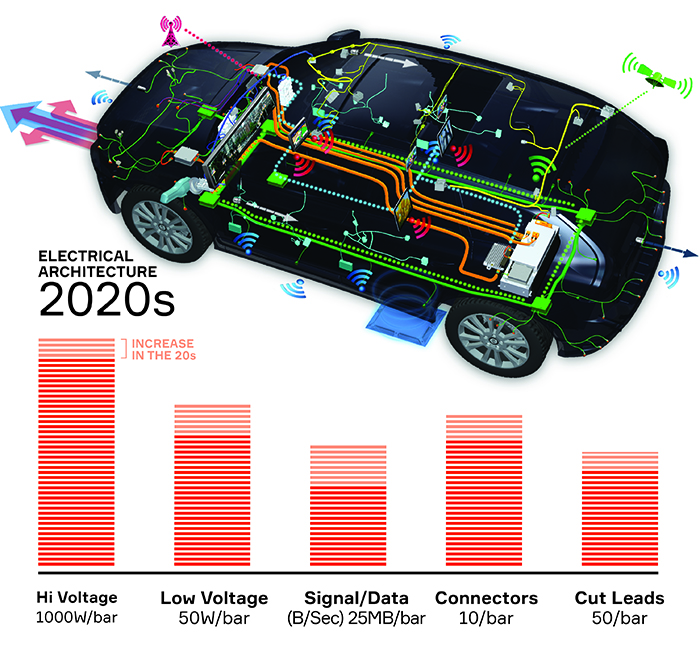
2030s: Advanced Integration
Safe, Green, Connected, All at the Same Time
- Multi-voltage domains bring more layers of device electrification
- Autonomous driving features create additional high-speed data networks
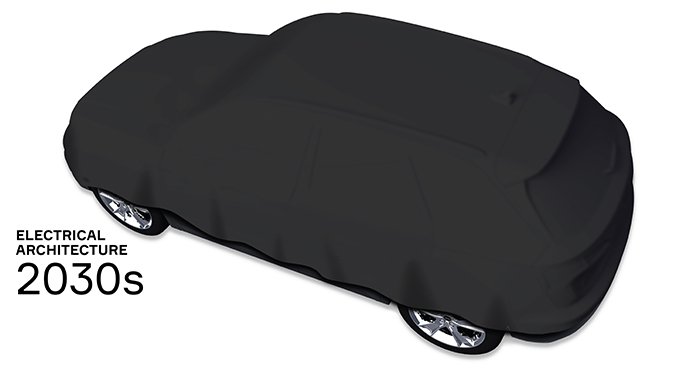
The pictures tell the story.
More features means more computing power, more data and more power distribution than ever before. And as the car becomes a supercomputer, with more and more features and connectivity, its architecture or foundation needs to change radically. The
historical vehicle architecture approach no longer works – it can’t support the growth in content and complexity.
This is where Aptiv’s expertise in smart architectures comes in. Aptiv’s Smart Vehicle Architecture™ (SVA) incorporates the full suite of our technology and brings it together through our systems integration expertise. We are unique in that we can integrate whole systems through SVA™, which enable all the electrification, active safety, automation, and connectivity, driving this new mobility.
We focus our efforts in four key areas; software, sensing and compute platforms, data and power distribution and connected services – all of which are foundational elements of Aptiv’s smart vehicle architecture.
What does this mean for autonomous driving? We can deliver an integrated vehicle system that controls each critical task needed to achieve higher levels of autonomy. Autonomous driving requires Automotive Safety Integrity Level D for fail-safe operation. This drives an electrical architecture break, and with it, deep implications on each of the three critical system levels: Power Distribution,
Networking and Compute.
Aptiv’s smart vehicle architecture has a three-layer fail operational design. This approach to system design considers power failure, network failure and even compute failure. It also has the ability to dynamically
re-route power, network traffic and even decision making to bring an autonomous car to a safe stop. Our extensive system design expertise covering all three layers delivers the necessary IP for fail-safe operation, the foundation for any smart vehicle
architecture.
Learn more about Aptiv’s Smart Vehicle Architecture